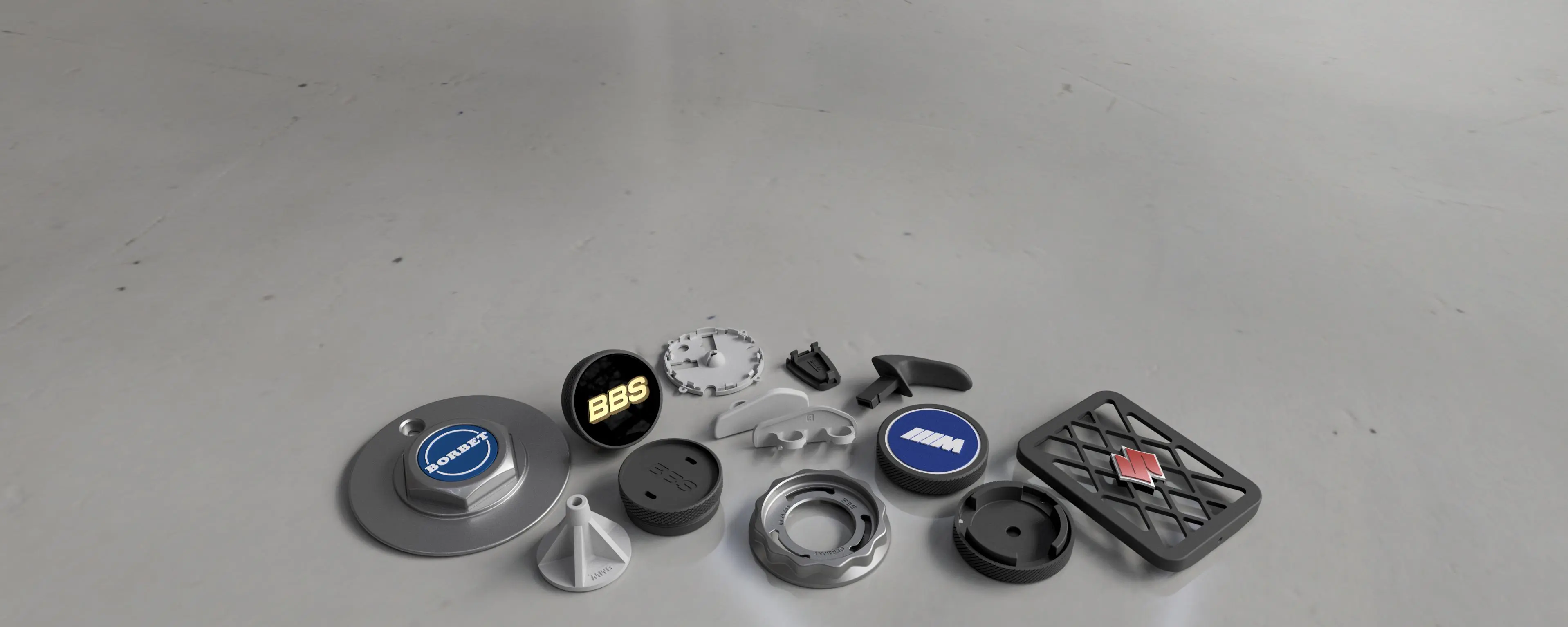
Our Bestsellers
Custom BBS center caps, unique snorkel intake grills, BMW retrofit/repair wiring harnesses, side mirror repair kits, and many other spare parts. Our products are meticulously crafted with unmatched attention to surface quality and precision.
Reviews on eBay, Wallapop, and Etsy: Over 300 Sales and 5-Star Ratings
Discover why over 300 customers on eBay, Wallapop, and Etsy rate us with 5 stars. With 100% positive feedback and a successful sales history, we ensure customer satisfaction across all platforms.
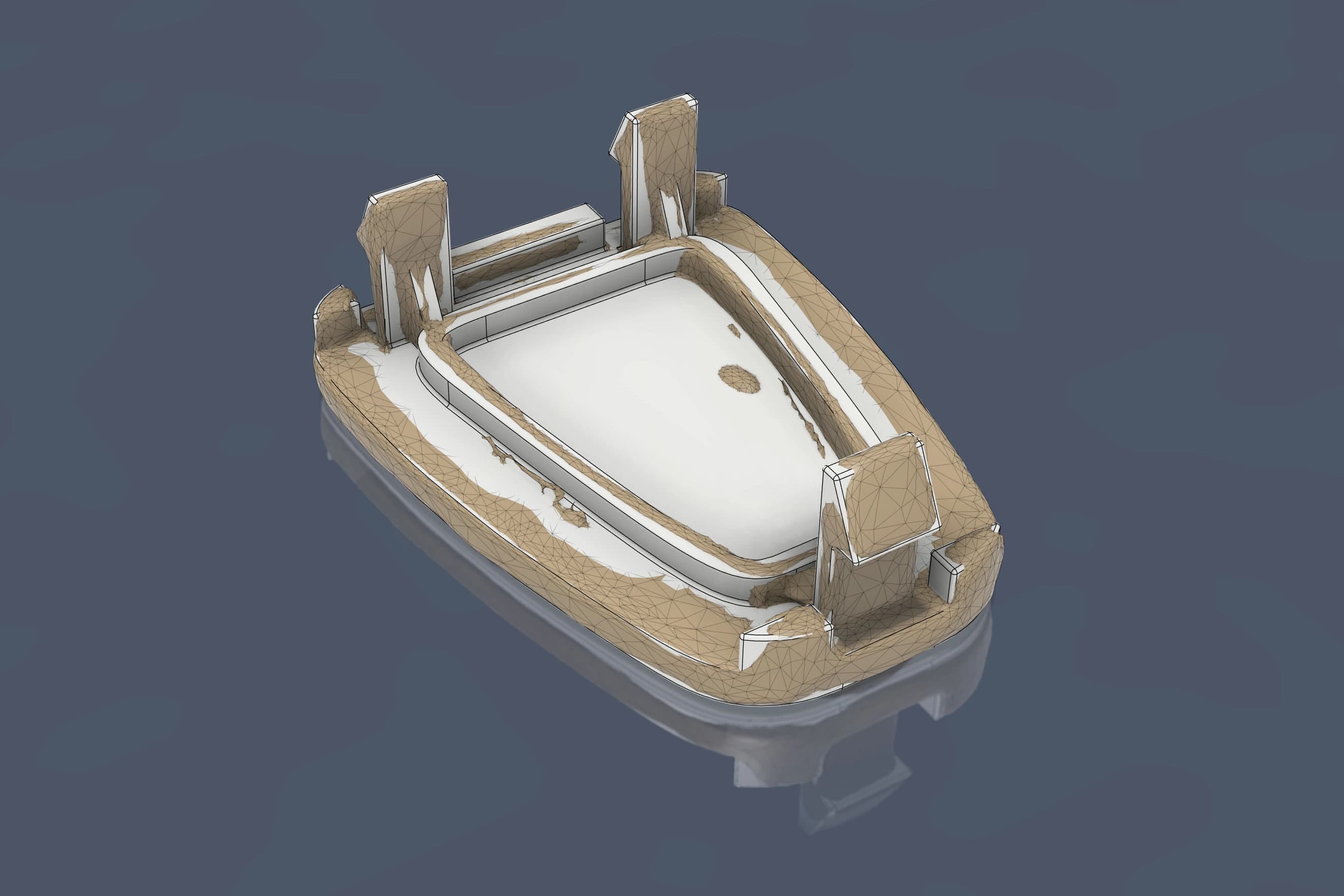
Design
Starting from a scan of the OEM part, we move to the CAD modelling to reproduce every surface. 3D scanning allows us to achieve excellent dimensional accuracy but we don’t stop there, we also introduce improvements in those areas where the initial component was deficient.
All our parts are designed from scratch. There’s a big investment in time for every reference and while this may reduce the volume of our catalog, we ensure that every design is fine-tuned so we can deliver high quality products.
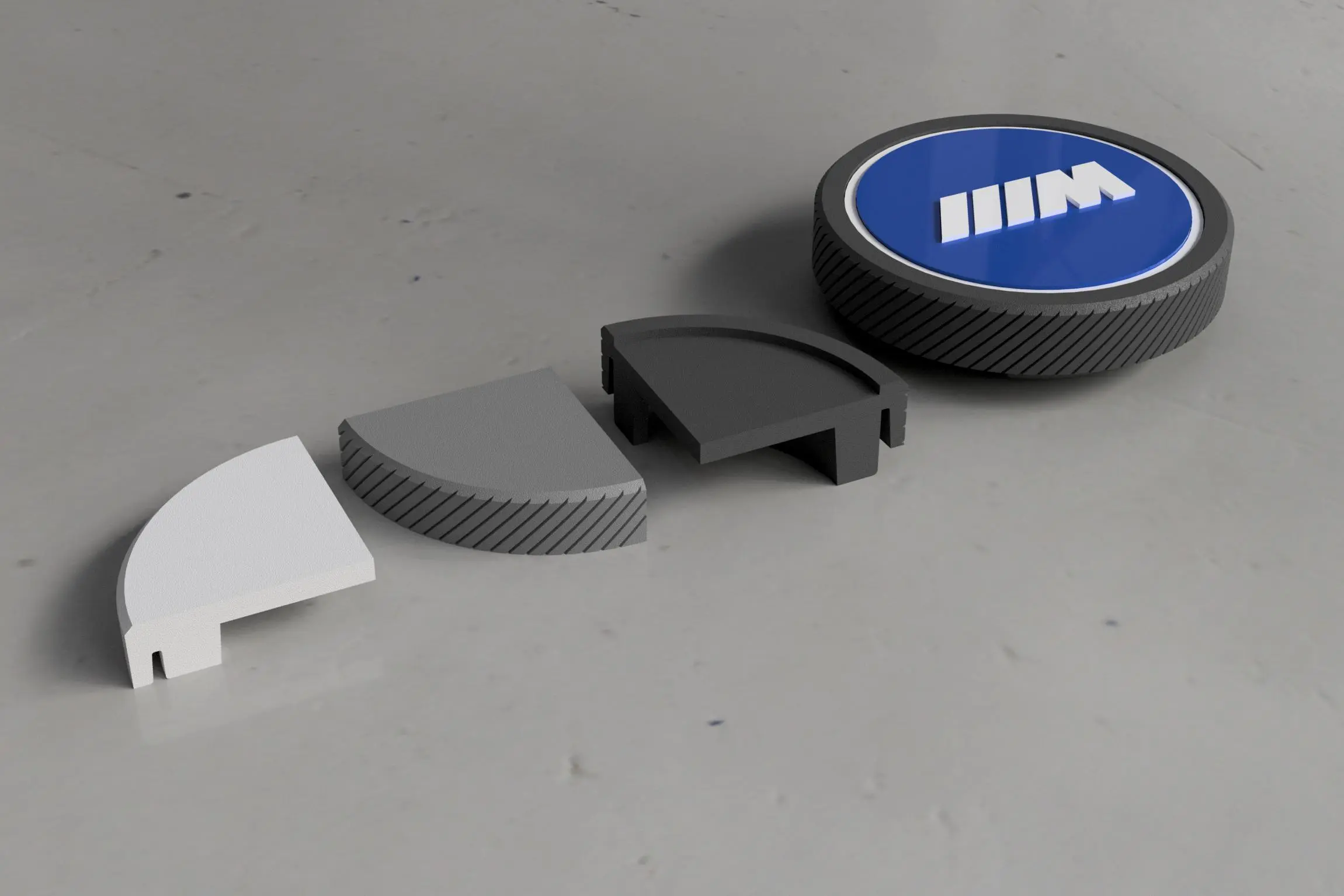
Prototyping
We develop multiple prototypes through each design iteration. All of our products had been test-fitted in real life before making them available for you.
At this stage we also study the mechanical endurance of our parts using the final material and come back to the design environment to make any required adjustments.
Moving forward with final manufacturing is not an option until every detail is flawless.
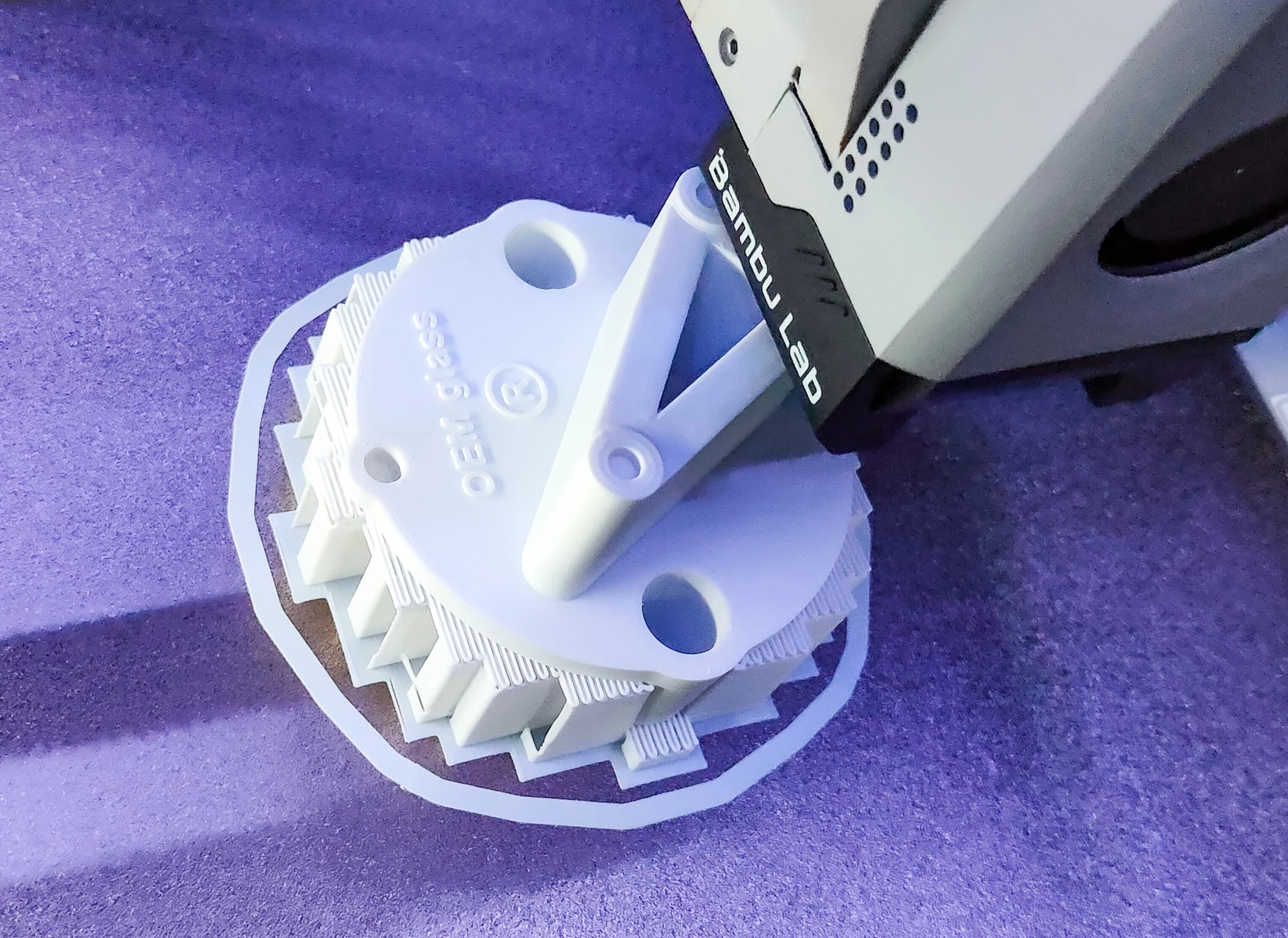
Manufacturing
Thanks to the latest 3D printing machines with advanced FDM capabilities, we bring our designs to life using materials that match or exceed the mechanical specifications of the original parts.
At J0sh 911, we carefully select every printing parameter considering not only the appearance of the part, but the modulus and orientation of the loads it will endure.
Additionally, we combine alternative manufacturing methods for those parts where the looks matter most.
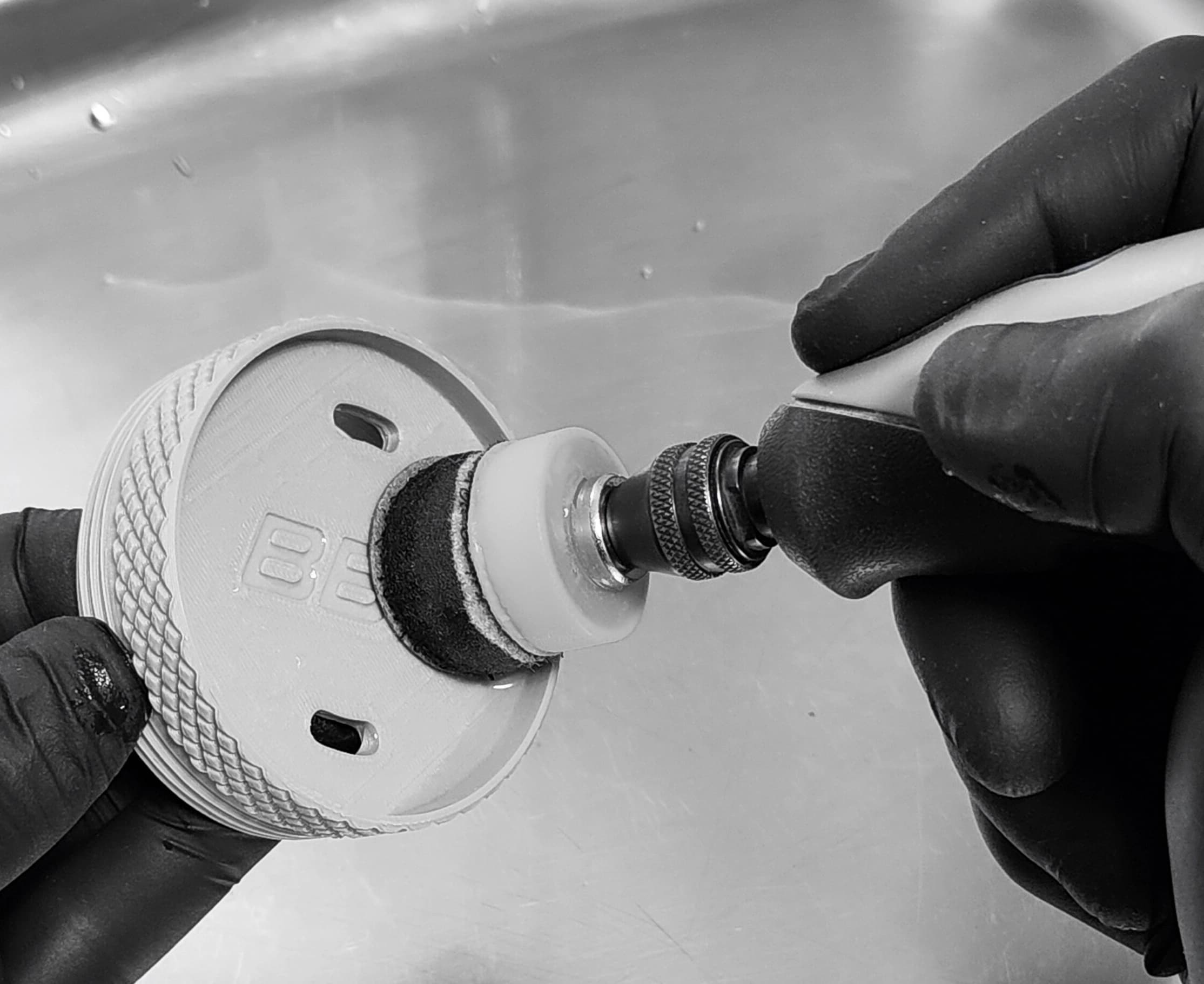
Post-processing
Even though FDM (Fused Deposition Modeling) technology cannot offer the surface quality of an injection-molded part right out of the box, we achieve comparable results through a meticulous post-processing procedure involving multiple sanding steps and the addition of varnish on most of our items.
Our materials
Having a quality design paired with the latest manufacturing techniques means nothing if you dont select the correct material for every task. So we take this very seriously
Mechanical properties
We only use engineering thermoplastics with high tensile and compressive strength to create our parts. At the same time, we reinforce the structures of our designs to achieve equivalent or superior mechanical properties to those of parts made by industrial injection molding processes.
Each part has different mechanical requirements and each geometry requires an independent analysis to select the most suitable material according to its manufacturability.
Heat Resistance
As a rule of thumb we dont use PLA, PETG or any of their derivatives for car parts. Those are the materials most of the people work with and they're great for cosmetic objects sitting in your desk but they won't last more than a few hours under direct sunlight.
Even ABS suffers degradation with UV exposure if not painted so we focus on ASA, PP, PC or PA and select their fiber reinforced variants when needed.